Fun Tips About Should Labour Be Included In COGS
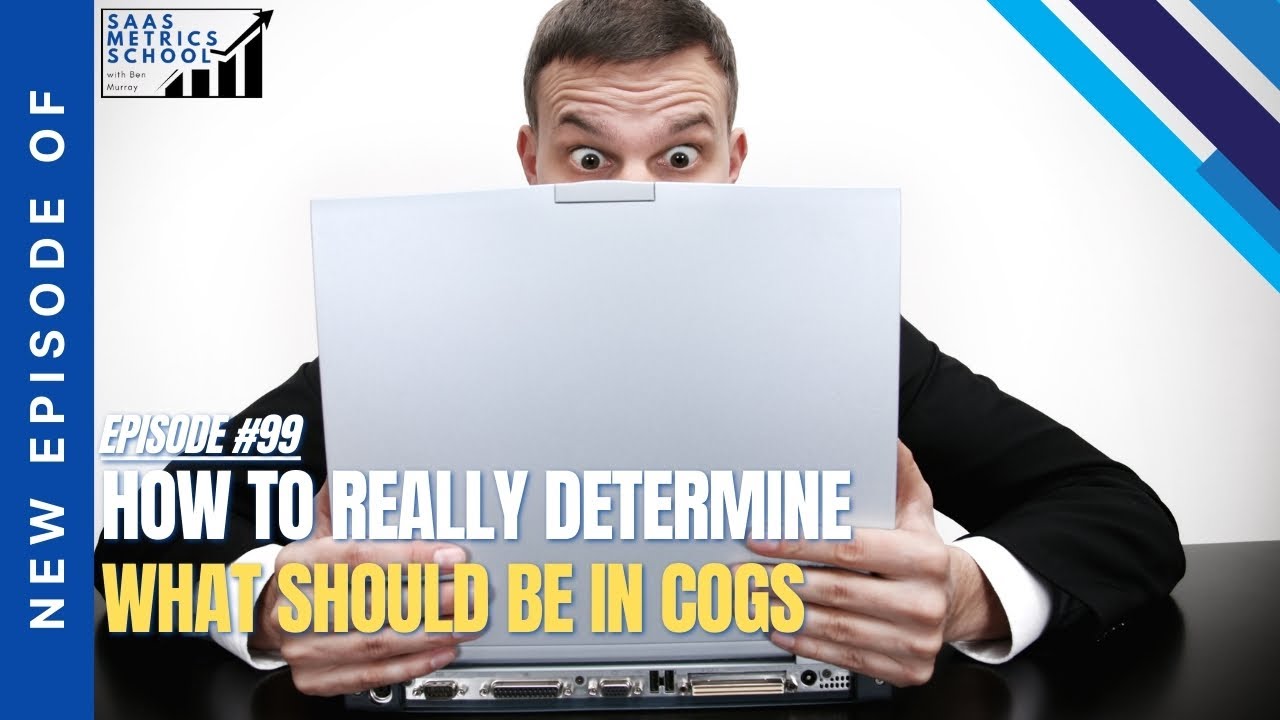
The Curious Case of Labour in COGS
1. What's COGS, Anyway? A Quick Refresher
Alright, let's talk shop. COGS, or Cost of Goods Sold, is a big deal for any business that deals with, well, goods! It's basically the direct cost of producing the products your company sells. Think raw materials, direct labour, and manufacturing overhead. It's a key figure because it directly impacts your gross profit — the money left over after subtracting COGS from your revenue. Mess it up, and your financial picture gets a little blurry. It's the financial equivalent of forgetting your glasses. You know things are there, but the details? Fuzzy.
Now, imagine you're baking cookies. The flour, sugar, chocolate chips — those are your raw materials. The electricity powering your oven? That's manufacturing overhead. And the hours you spend mixing, baking, and cleaning up? That's where things get interesting, and we stumble into the debate of whether or not to include labour in COGS. After all, if you weren't there doing the cookie magic, those cookies wouldn't exist, right? So, shouldn't your time factor into the cost of each delicious batch?
Companies use COGS to understand their profitability. By calculating exactly how much it costs to make each item, they can then make smart decisions on pricing, sourcing and production levels. If your COGS are too high, youre losing money without even realizing it. Thats like perpetually paying too much for movie tickets — it slowly drains your bank account!
COGS is more than just a number on a spreadsheet. It is the lifeline that any good company has to understand its operational performance. Accurate COGS calculation is crucial for tax reporting, financial analysis, and making sound business decisions. Misreporting can get companies into trouble with tax agencies and can seriously misrepresent its profitability. Its essential to get the COGS calculation right to have an accurate snapshot of your finances and stay out of trouble.
2. The Great Labour Debate
Here's where the plot thickens. The key to figuring out if labour belongs in COGS hinges on whether it's direct or indirect. Direct labour is the work that's directly involved in creating the product. So, in our cookie example, your baking time would be direct labour. Indirect labour, on the other hand, supports the production process but isn't directly involved. Think the supervisor overseeing the bakery, or the cleaning crew keeping everything spick and span. Their wages are typically considered part of manufacturing overhead, not direct labour.
The general rule of thumb is that only direct labour makes the COGS cut. If someone's hands are on the product, actively transforming it from raw materials into a finished good, then their wages are usually included. But if they're in a support role, their cost gets lumped in with other overhead expenses. This distinction is important because it helps accurately reflect the true cost of production. If we start including every single employee's salary in COGS, the numbers get skewed, and it becomes harder to pinpoint areas where we can improve efficiency or cut costs.
Imagine trying to run a lemonade stand and including your Netflix subscription as part of the COGS. It wouldnt really make sense, would it? While Netflix might be your inspiration, it doesnt directly contribute to the lemonade itself. Similarly, the same principle applies when separating direct labour costs from indirect labour costs.
Moreover, the method of payment also plays a part in this consideration. Is your labor force paid an hourly wage, a monthly salary, or a piece-rate system (where they get paid for each unit produced)? Hourly and piece-rate wages are generally easier to allocate to COGS than fixed salaries. The more direct and traceable the labor cost, the easier it is to include it as part of COGS, providing a clearer picture of the true production costs.
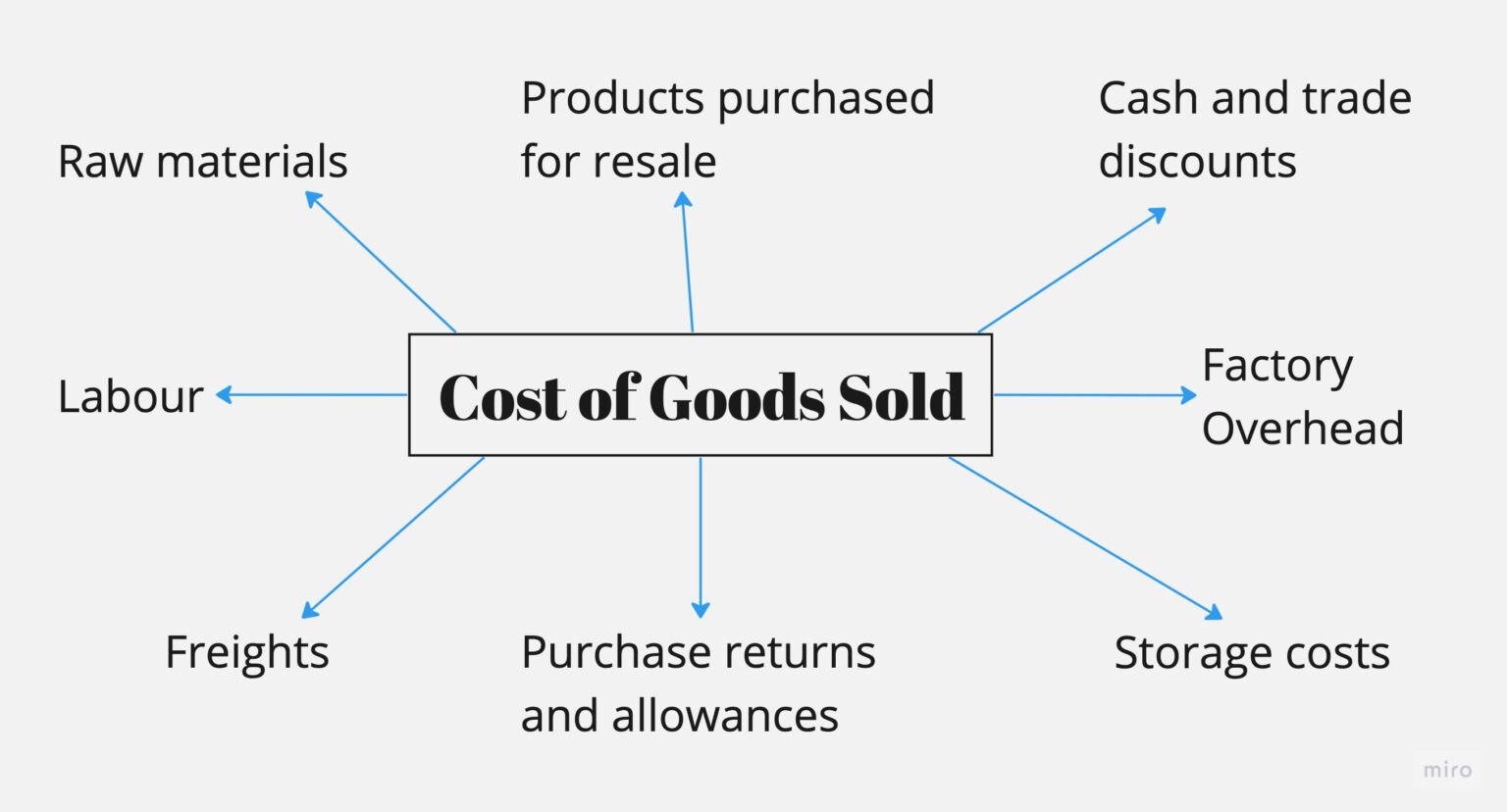
Cost Of Goods Sold Definition, Calculation, And More Glossary By
Navigating the Grey Areas and Industry Standards
3. Industry Practices
Okay, so we know the theory, but what about real life? Well, industry practices can vary. Some industries, like manufacturing, almost always include direct labour in COGS. It's just part of the game. Others, particularly service-based businesses, might not have a COGS at all (since they're selling services, not tangible goods). It is always good to refer to industry-specific guidelines to ensure compliance and best practices.
For example, a construction company would definitely include the wages of the carpenters and bricklayers in COGS. But a software company? Probably not. Their main cost is likely research and development, which is treated differently. It all boils down to understanding your industry and the specific nature of your business. Think of it as knowing which fork to use at a fancy dinner — it depends on the course!
And let's not forget about Generally Accepted Accounting Principles (GAAP). GAAP provides a framework for financial reporting. So, what does GAAP say about it? It says, if you can accurately trace and allocate the labour cost directly to the production of goods, then it belongs in COGS. But if it's tricky to allocate, you might be better off treating it as an operating expense. Basically, GAAP wants you to be reasonable and transparent in your accounting practices.
Also, keeping up with industry benchmarks can provide valuable insights into how your competitors are handling labor costs in COGS. This allows you to compare your companys practices and identify potential areas for improvement or cost-saving strategies. By aligning with or strategically deviating from industry standards, you can better position your business for competitive advantage.
4. The Importance of Consistency
Whatever you decide, consistency is key. Once you've chosen a method for treating labour costs, stick with it. Don't flip-flop back and forth, because that'll make your financial statements a confusing mess. Consistency makes it easier to compare your results over time and track your progress. It's like having a favorite coffee shop — you know what to expect, and you can easily spot when something's off.
Inconsistent accounting practices not only muddy your financial waters, but they can also raise red flags for auditors and investors. Imagine trying to decipher a financial report that changes its methodology every quarter. It's a recipe for frustration and distrust. So, establish a clear policy for how you treat labour costs in COGS, document it thoroughly, and follow it religiously.
Further, be sure to keep a record of your decision-making process, explaining the rationale behind your treatment of labor costs. This documentation will come in handy during audits, providing auditors with a clear understanding of your accounting choices and ensuring compliance with accounting standards. Transparency and documentation are your best friends when it comes to financial reporting.
Consistency also allows for a more accurate trend analysis, allowing you to see, and track the impact of any new business strategies. Without consistent practices, those trend analysis becomes incredibly difficult. If you decide to change the policy, make sure you can articulate the reasons for the change, and that you document it thoroughly.
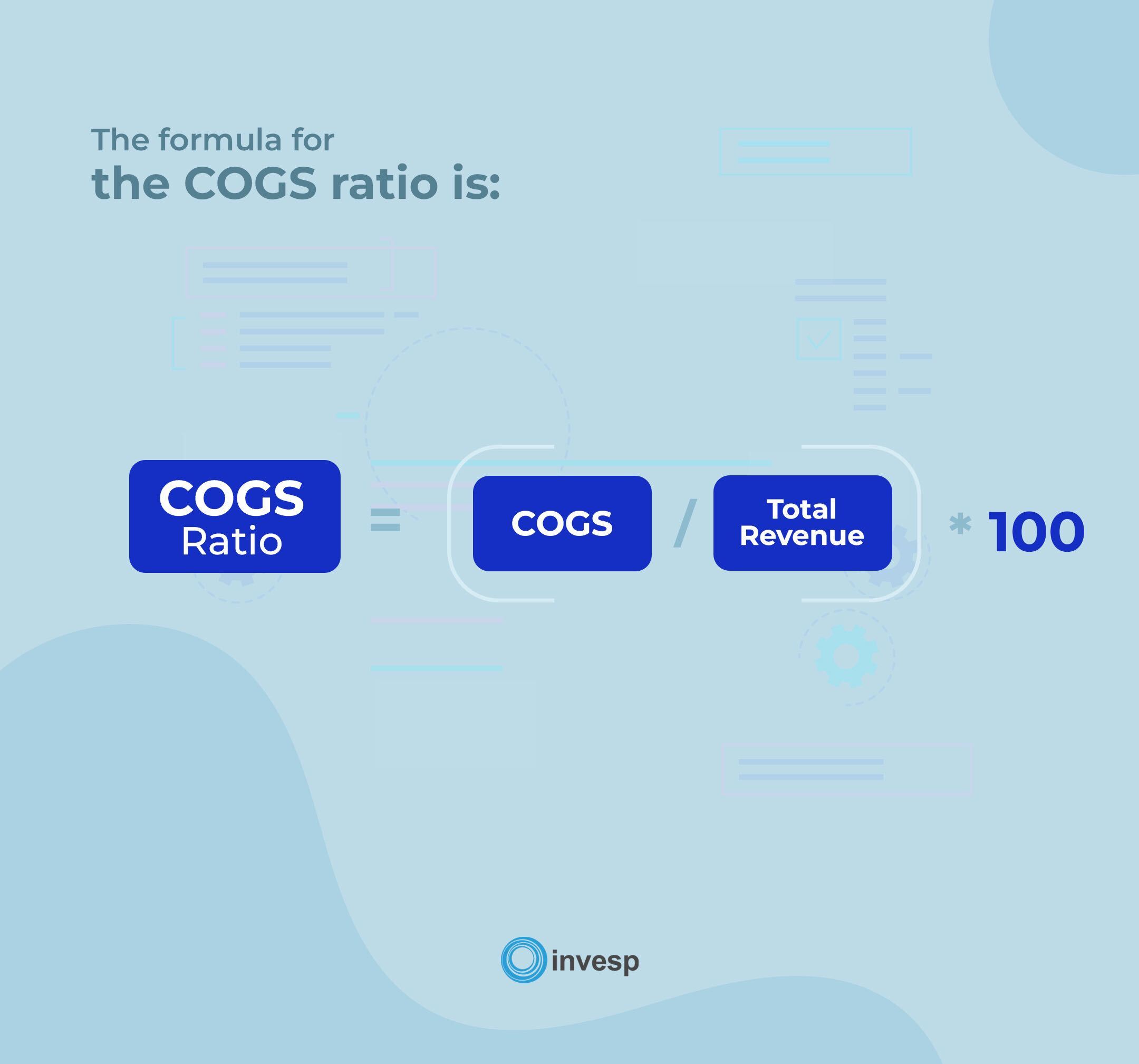
COGS Formula 101 Essential Insights For Entrepreneurs Invesp
Potential Pitfalls and How to Avoid Them
5. Over- or Under-Allocation
One of the biggest challenges is figuring out how much of an employee's time actually goes into direct labour. If someone spends half their time assembling products and the other half doing something else, you need to allocate their wages accordingly. Over-allocating labour costs to COGS can inflate your cost of goods sold, reducing your gross profit and making your business look less profitable than it actually is.
On the flip side, under-allocating labour costs to COGS can make your business appear more profitable in the short term, but it can also mask inefficiencies and potential problems in your production process. It's like sweeping dust under the rug — it might look clean on the surface, but the mess is still there. The goal is to find the sweet spot, where you're accurately reflecting the true cost of producing your goods.
To avoid these pitfalls, use time tracking systems or detailed employee logs to track how employees spend their time. This helps you accurately allocate labour costs to COGS and avoid making inaccurate assumptions. These systems can be simple spreadsheets or sophisticated software, depending on the size and complexity of your business. The more data you have, the better equipped youll be to make informed decisions.
Another pitfall to avoid is neglecting to update your labor cost allocations as your business changes. As you grow or shift your production methods, you need to re-evaluate how you're allocating labor costs to ensure accuracy. Its a continuous process, not a one-time task. Adaptability is key to maintaining accurate financial reporting and making informed business decisions.
6. The Dreaded Audit
Let's face it, nobody loves being audited. But if you've got your ducks in a row, it shouldn't be a nightmare. Make sure you have clear documentation of your policies for treating labour costs, as well as detailed records to support your calculations. Auditors will want to see that you're following GAAP and that your numbers are accurate and consistent.
Good accounting software can be a lifesaver here. It can automate many of the calculations and reports you need for an audit, making the whole process much smoother. It's like having a personal assistant who's a whiz with spreadsheets! But even with the best software, it's important to understand the underlying principles and be able to explain your decisions to the auditors. You don't want to rely solely on the software without knowing why it's doing what it's doing.
One effective way to prepare for an audit is to conduct internal audits periodically. This allows you to identify any potential issues or errors before the external auditors arrive. It's like practicing for a big game — it gives you the chance to iron out any wrinkles and build confidence. Regular internal audits can also help you identify areas where you can improve your accounting practices and strengthen your financial controls.
And remember, honesty is always the best policy. If you've made a mistake, own up to it and be prepared to explain how you're going to fix it. Auditors appreciate transparency and a willingness to correct errors. Trying to hide something will only make things worse. It's better to be upfront and work with the auditors to resolve any issues.
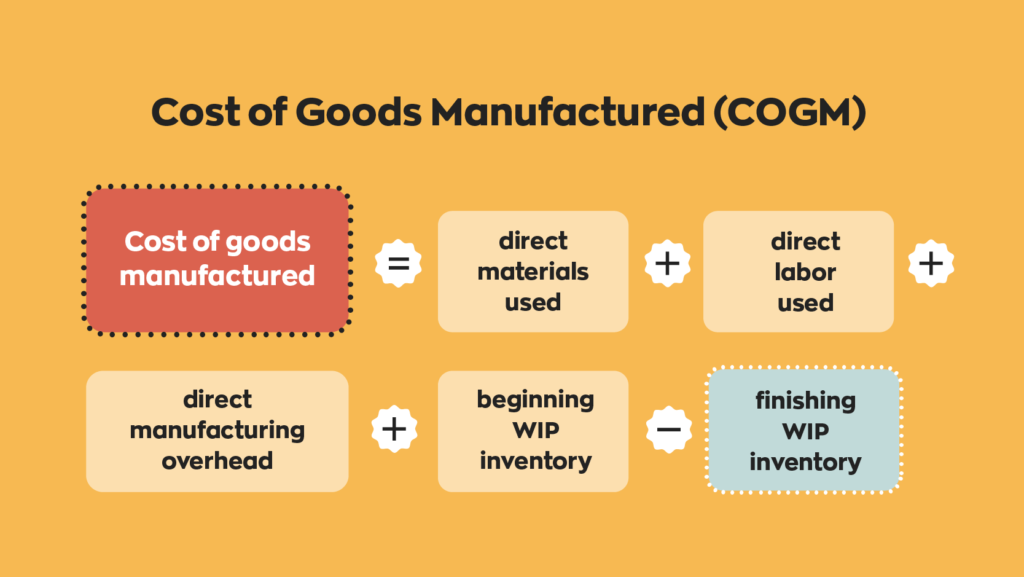
Calculate Your Cost Of Goods Manufactured With This Formula
Real-World Examples
7. Scenario 1
Imagine a small craft brewery. The brewers who are actually brewing the beer? Their wages would definitely be included in COGS. The marketing team, on the other hand, wouldn't be. Their salaries would be considered operating expenses. It's a pretty clear-cut example of direct versus indirect labour.
But what about the person who cleans the brewing equipment? That's a bit trickier. If they're dedicated solely to cleaning the equipment used in the brewing process, their wages might be considered part of manufacturing overhead, which is included in COGS. But if they also clean the restrooms and office spaces, their wages would need to be allocated accordingly. It's all about tracing the cost back to the production process as directly as possible.
Also, if the brewery uses a quality control specialist to taste and test the beer as part of the brewing process, their wages should likely be included in COGS as well. Ensuring the quality of the product is an integral part of production, so the cost of quality control can be justifiably included.
By carefully categorizing and allocating labor costs, the brewery can gain a clearer understanding of the true cost of producing each pint of beer. This insight can then be used to make informed decisions about pricing, production levels, and overall business strategy.
8. Scenario 2
Now picture a small shop that creates custom furniture. The carpenters and finishers who are building the furniture? Absolutely, their wages go into COGS. The salesperson who takes the orders? Nope, their commission is a sales expense. It is important to understand each roles in the company to avoid mistake.
Let's say the shop owner also spends some time building furniture. They would need to allocate their salary accordingly. If 60% of their time is spent on direct labour, then 60% of their salary would be included in COGS. The remaining 40% would be treated as an operating expense.
Don't forget about the cost of apprenticeships! If the furniture maker is training new apprentices, the wages paid to the apprentices can also be included in COGS, as they are actively involved in the production process. Providing training directly enhances the capacity to build the furniture, justifying its inclusion.
Furthermore, the furniture maker should factor in the cost of any benefits provided to their direct labor employees, such as health insurance or retirement contributions. These benefits are part of the overall labor cost and should be allocated to COGS accordingly. Total cost of the employee must be taken into account.
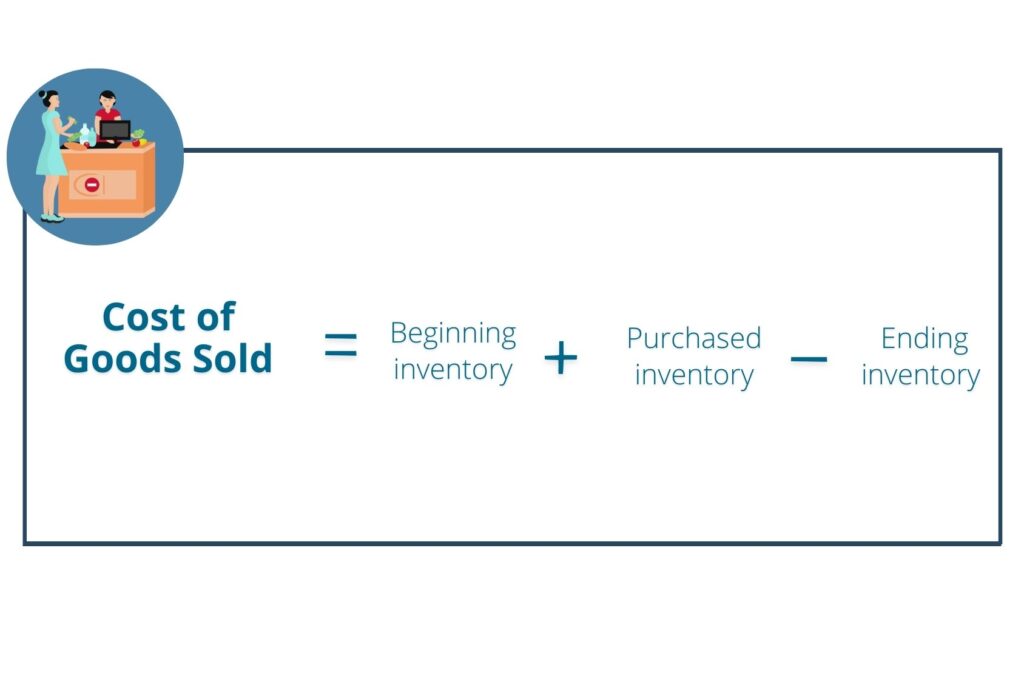
Inventory Accounting 101 The Basics You Need To Know
FAQs
9. Q
A: This is where it gets a little tricky. You'll need to estimate the percentage of time they spend on each activity and allocate their wages accordingly. Time tracking software or detailed employee logs can be helpful here. Be sure to document your method clearly.
10. Q
A: It depends. If the training is directly related to the production process, such as learning how to operate a new piece of equipment, then it can be included. But general training, like customer service skills, would be considered an operating expense.
11. Q
A: Changing accounting methods can have a significant impact on your financial statements. You'll need to disclose the change and its impact in your financial reports. It's a good idea to consult with an accountant before making any changes.
